What is an inventory cycle count (and how do you apply it)?
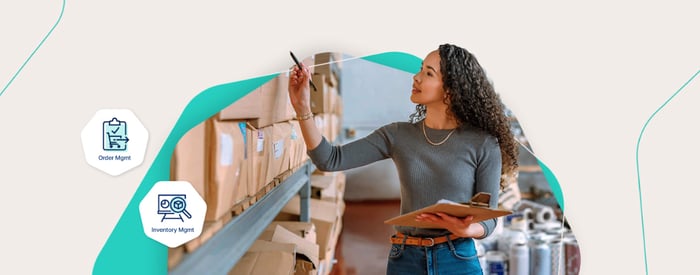
Auditing inventory is an undervalued aspect of the inventory management process and one of the most crucial. For warehouses to run efficiently, companies must regularly ensure that physical stock matches inventory records, which is easier said than done — especially if your inventory needs fluctuate due to demand shifts and business growth.
Inventory cycle counting is an inventory tracking method that companies use to verify that physical stock matches inventory records. Unlike periodic and perpetual inventory methods, cycle counting refers to a cyclical process that companies employ to avoid traditional audits and ensure inventory always gets accounted for.
Companies tend to prefer inventory cycle counting over traditional stocktaking processes. Full physical inventory counts, while necessary, are often time-consuming, profit-shrinking, and headache-inducing. Yet, most small businesses only use full physical inventory audits to take stock.
Below, we’ll show you what cycle counting is, how it can benefit your business, and reveal cycle counting best practices so you can manage your inventory efficiently.
Key Takeaways:
- Inventory cycle counting is the process of regularly counting small predetermined portions of your inventory over time.
- There are several inventory cycle counting methods, like control group, ABC analysis, random sample, cycle counting by usage, and the hybrid method.
- Regular inventory cycle counts can help small businesses optimize inventory performance by lowering costs
- While a physical count involves counting everything in the warehouse, an inventory cycle count is a more frequent count of certain selected items.
What is cycle counting?
Cycle counting is an alternative stocktaking process that involves regularly counting a small portion of your inventory over time instead of counting your entire inventory in one sitting.
While most businesses have to shut down or work overtime to perform full physical inventory audits, cycle counting allows businesses to update their inventory records without shutting down during business hours or after closing time, allowing you to keep processes in flow and maintain inventory control.
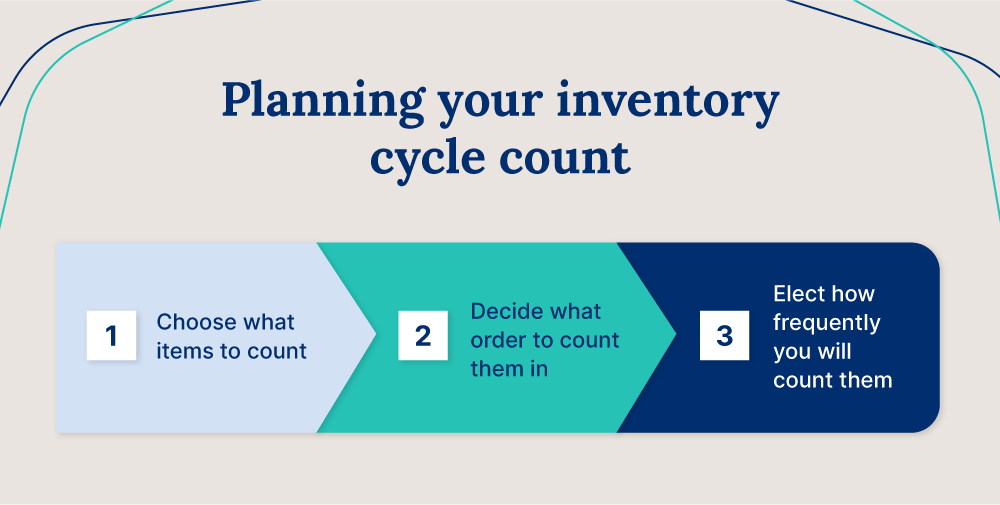
The cycle counting process itself is relatively simple:
- Choose which items need to be counted
- Determine the order you need to count them in
- Establish how often you’ll count
Later, we’ll explore the specifics of performing your cycle count.
Cycle Counting in Different Business Models
Cycle counting is a versatile inventory management practice that can benefit businesses across various industries. While the concept remains the same, the way cycle counting is implemented can differ significantly depending on the type of business. Here’s how cycle counting works in retail, warehouse management, and manufacturing, offering tailored insights into its industry-specific benefits.
Retail Industry
In the retail sector, cycle counting inventory helps ensure accurate inventory records, which are essential for maintaining stock levels and reducing shrinkage. Retailers often face challenges with frequent stockouts or overstocking, and cycle counting helps mitigate these risks by providing a continuous and accurate inventory count without needing a complete shutdown for a traditional physical inventory count. By conducting random cycle counting on high-turnover items or using an ABC cycle counting method (where high-value items are counted more frequently), retailers can optimize their stock and provide better customer service.
Warehouse Management
For warehouses, accurate warehouse cycle counting is crucial for efficient operations. Warehouses often deal with large quantities of inventory, spread across vast storage spaces. Here, cycle counting can help maintain real-time inventory accuracy, especially when integrated with cycle count software. This allows warehouse managers to reduce discrepancies and streamline daily operations by identifying inventory variance early on. Many warehouses implement cycle counting procedures that focus on areas with high inventory movement, ensuring that physical counting is conducted where it’s most needed, without disrupting regular operations.
Manufacturing Industry
In the manufacturing industry, cycle counting is crucial for maintaining inventory accuracy across various stages, from raw materials to finished goods. Cycle counting in this context ensures that manufacturers always have the right components for production without delays caused by stockouts or excess inventory. Manufacturers often use ABC cycle counting to prioritize high-value or frequently-used materials. Integrating cycle count software with manufacturing execution systems helps streamline inventory control and reduce disruptions in the production process. This approach is essential for optimizing production schedules and maintaining smooth operations.
Inventory cycle count methods
Depending on your business, warehouse management system, and products you sell, certain inventory cycle count methods may work better than others. Here are a few different inventory cycle count methods and examples of each.
1. Control group
Control group cycle counting is especially helpful for businesses using cycle counting for the first time because it allows you to test the process and uncover errors in your method before implementing it across your entire inventory.
With this method, you will choose a small group of items that will get counted many times over a short period. Once you can perform the cycle count without any errors and feel confident in your process, you can apply it to the rest of your inventory.
Example: A shoe retailer tests control group testing on shoe soles, an area the company is confident they have an accurate inventory. Once the process works well for soles, they apply control group cycle counting to the entire warehouse.
2. ABC analysis
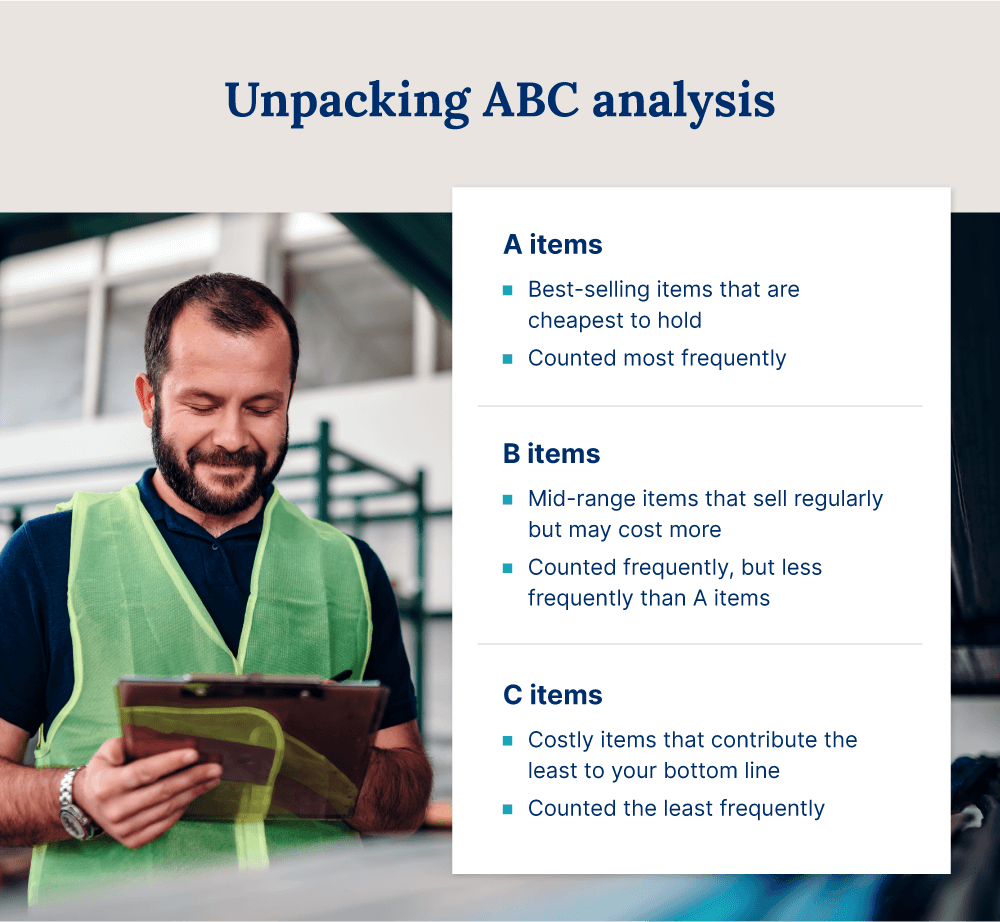
ABC analysis is a cycle counting method that involves sorting inventory into three categories based on how well they sell and how much they cost to hold. The categories include:
- A items: Best-selling items that don’t take up all your warehouse space or cost
- B items: Mid-range items that sell regularly but may cost more than A-items to hold
- C items: The rest of your inventory that makes up the bulk of your inventory costs while contributing the least to your bottom line
The item’s category dictates how frequently it gets counted during the process.
- A items: Counted most frequently (multiple times throughout the year)
- B items: Counted somewhat frequently (a few times throughout the year)
- C items: Counted infrequently (once or twice throughout the year)
Example: A hoodie company is categorizing their hoodies for their fall demand season. Category A hoodies are the most popular and will be in high demand when fall begins. Category B hoodies are less popular but still integral to the company. Category C hoodies are low-value, and effort doesn’t need to be put into selling them.
3. Random sample
In warehouses with many similar items, you can randomly select items to be counted. Random sample cycle counting consists of two different approaches.
- Constant population counting: Items are returned to the general population of the warehouse after getting counted, which means they could be selected to be counted again.
- Diminished population counting: Items remain outside the general population after getting counted, ensuring you don’t count them again.
The method you select will largely depend on the frequency you count your items. If you do cycle counts often, constant population counting likely makes the most sense since duplications won’t matter much in the long run.
Example: A makeup company counts stock weekly using the constant population counting method. Since the staff counts certain items every seven days, it doesn’t make a difference that they’re returning items to the general population.
4. Cycle counting by usage
This is one of the simplest forms of cycle count as it relies on counting frequently used items. In this method:
- Items get sorted as per the frequency of workers accessing them.
- Storage racks get arranged accordingly, so you don’t need to assign dedicated staff hours.
- High-consumption items get prioritized, and the complexity is relatively negligible. However, it does not differentiate the cost of the stored components.
Cycle counting by usage overlooks the impact of any miscalculation on the production process or financial losses. As a result, this method only makes sense for low-value, comprehensive inventory-carrying companies.
Example: A chip company sells its barbeque flavor well but struggles to see its salt and vinegar flavor. As a result, staff counts the barbeque flavor daily but only counts the salt and vinegar flavor monthly.
5. Hybrid method
Hybrid methods are formed by combining ABC analysis with other methods. This includes focusing on vital parts, production line vulnerability, reorder costs, economic order quantity (EOQ), sales, hazards, and other relevant factors.
This approach varies from company to company and is usually a tailored procedure. In most cases, companies will implement the hybrid method because they have a specific product that doesn’t fit nicely into one of the categories within the ABC structure.
Example: The same hoodie company from above introduces a new sustainably-made hoodie that doesn’t sell as well as category A hoodies but is costlier to produce and hold. As a result, you use cycle counting by usage for the new model but continue using ABC analysis for all the other hoodies.
6. Integration with Inventory Management Systems
One of the key trends in modern inventory management is the integration of cycle counting with inventory management software or ERP systems. Integrating cycle counting with these systems offers businesses real-time visibility and improved accuracy, making it easier to manage stock levels, reduce discrepancies, and enhance decision-making capabilities.
Benefits of Cycle Counting Integration
By integrating cycle counting with an inventory management system, businesses can:
- Achieve Real-Time Accuracy: Inventory management software automates the process of updating stock levels after every stock count, ensuring that your records are always accurate and up to date. This reduces the chance of errors that occur with manual data entry and provides real-time insights into stock availability.
- Streamline Daily Operations: Automation allows businesses to conduct cycle counting inventory during daily operations without disrupting them. With integrated systems, businesses can schedule counts during low-activity periods, ensuring that critical items are always available without halting business operations.
- Generate Detailed Reports: Integration enables businesses to generate detailed reports on inventory variance, discrepancies, and stock movement. This not only helps maintain accurate inventory records but also enables better forecasting and inventory planning based on real-time data.
- Enhanced ABC Cycle Counting: ABC cycle counting becomes much more efficient with integrated systems. Businesses can automatically categorize inventory based on value and turnover, ensuring that the most critical items are counted more frequently.
Combining Cycle Counting with ERP Integration
For larger businesses, integrating cycle counting with enterprise resource planning (ERP) systems is a game-changer. ERP integration allows for a seamless flow of inventory data across multiple departments, ensuring that sales, finance, and operations teams are all working with accurate information. This is particularly important for businesses with complex supply chains or multiple warehouses. The ERP integration ensures that all cycle counts are reflected in the overall inventory data, helping maintain consistent and reliable stock records across the entire organization.
By incorporating cycle counting into an automated system, businesses can not only improve inventory counting but also enhance overall efficiency, reduce labor costs, and improve decision-making with better data visibility.
7. Inventory cycle count best practices
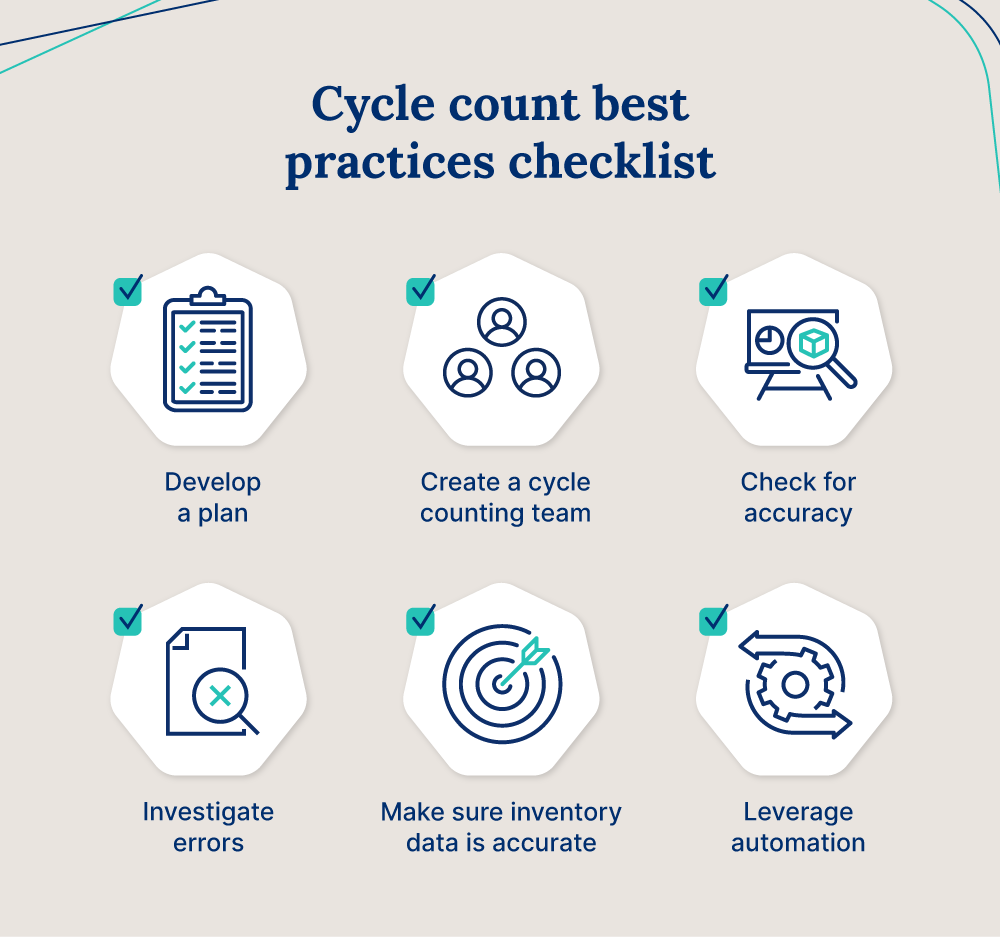
While the method you select will guide the inventory cycle count process, it’s important to follow a few universal best practices when conducting your count. Some of these include:
1. Developing a plan for routine cycle counting
Before jumping into a cycle counting routine, you should detail:
- Exactly what items you’ll count
- How often you’ll count those items
- How frequently you’ll conduct your counts
You could make cycle counting a part of your daily routine, or choose one day every week to do it. Whatever your plan is, write it down and stick to it.
2. Creating a cycle counting team
You have to be on the frontlines implementing cycle counting, but you don’t have to do the cycle counting yourself.
Instead, you should assemble a team to perform the actual counting. Your team can consist of one other person or a group of employees.
Regardless, make sure they understand their job responsibilities, the layout of your warehouse, and how to use the tools for counting your inventory.
3. Checking for accuracy
When you have staff physically counting inventory, it leaves the door open for human error. Double-checking the count is a good way to get the most accurate number. While it may feel wasteful to dedicate this much time to a QA process, inaccurate counts can lead to more significant business interruptions if not identified quickly.
You can check in a couple of different ways. For example, if the morning staff does the initial count, you can also ask the afternoon staff to do a count to verify the numbers. You can also have supervisors do a second count after the staff completes theirs.
4. Make sure inventory data is current
Keeping your inventory records current is equally as important as keeping a pulse on your physical inventory.
Before you begin your cycle count, verify your inventory records are up-to-date, so you cross-check physical inventory against the most current inventory information.
5. Investigate errors
If you notice that physical inventory does not match your inventory records, dig into the issue and find where the problem lies. Investigating errors in your cycle count may reveal other issues related to your inventory management process.
Some common errors include:
- Human errors, like miscounting
- Incorrect data entry
- Disorganized warehouse
Inventory management software automates data entry and updates automatically, making you less likely to experience errors during cycle counting.
6. Leverage automation
Automated inventory management gives you the capability to increase the accuracy of your counts by:
- Automatically updating inventory information
- Running regular inventory reports
- Identifying low stock
Leveraging automation in your cycle counts can speed up the process down the road, as errors are far less likely to occur with comprehensive software keeping tracking of your inventory data.
Automate your inventory management with Cin7
Benefits of an inventory cycle count
Having accurate inventory information is necessary for the health and growth of a small business. However, doing regular cycle counts has some lesser-known benefits. Some of these include:
- Minimizing disruptions to business operations: You never want to pause business operations because of an inventory issue. Regular cycle counts ensure you stay in the flow.
- Saving costs: If you select a method that works well for your specific business needs, you’ll gain stock information that can help you place smarter and more strategic reorders, thus improving your inventory turnover ratio.
- Providing real-time insight into inventory levels: The more frequently you perform inventory counts, the greater your awareness of what’s in your warehouse and what your inventory levels look like.
Inventory cycle count vs. physical count
The main difference between inventory cycle counts and physical counts is the count frequency and the items getting counted.
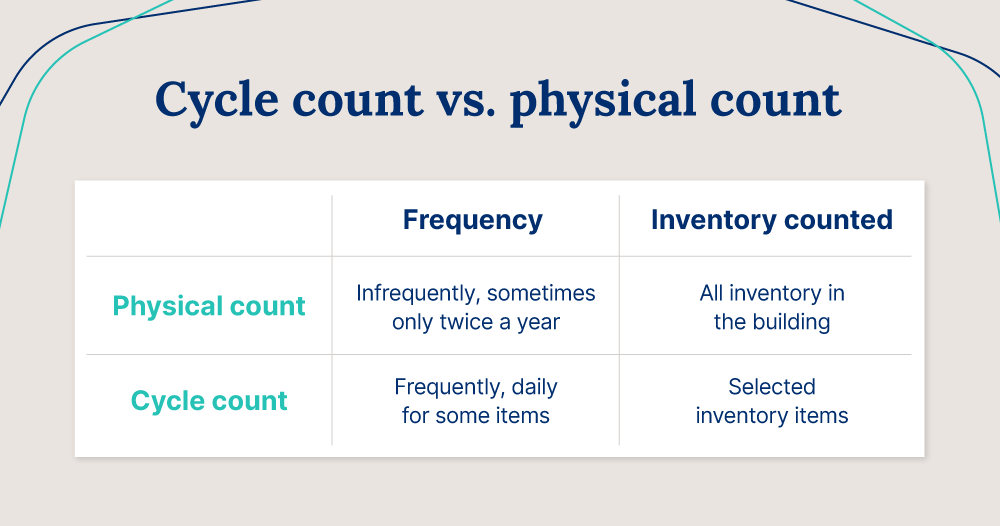
Physical counts:
- Are more structured than inventory cycle counts
- Always happen twice a year
- Involve counting all the stock in the building
Inventory cycle counts:
- Are designed according to your chosen method
- Can happen as frequently as every day
- Involve counting a predetermined number of items
Frequently asked questions
Still have questions before launching into your cycle count? Here are some of the most common questions (and answers) about implementing cycle count in inventory management.
What is the 80-20 rule in cycle counting?
The 80-20 rule is a principle that claims 20% of warehouse parts are responsible for 80% of sales.
In cycle counting, the 80-20 rule justifies that certain items should get counted more regularly, as some are far more significant to a business’s bottom line than others.
How often should you cycle count inventory?
You should conduct a full cycle count at least once a quarter, but you may want to perform counts of high-priority items as often as every day.
More regular counts can also help you avoid doing time-consuming full counts at the end of each month or quarter.
What is an example of a cycle count?
Say, for example, you have 1,000 stock-keeping units (SKUs) that you need to count monthly.
An example of an inventory cycle count could be the process of counting the items in 3 to 4 of each SKU daily.
What is a good cycle count accuracy?
A good cycle count accuracy is between 95%-98%. Anything less than 95% would likely require you to do a full physical inventory count.
For companies carrying high volumes of inventory, it’s normal to come in slightly south of 100%, such as 97% or 98%. Miniscule differences like this don’t require you to conduct a full physical inventory count.
Create efficiency with regular cycle counts
Inventory cycle counts are a vital part of achieving inventory efficiency and Connected Inventory Performance, but they’re only one piece of the puzzle.
With comprehensive inventory management software, you can ensure more accurate inventory counts and make informed decisions through your cycle counts. Coupled with a robust tool, your inventory cycle counts can go from monotonous tasks to strategies that bolster business growth.