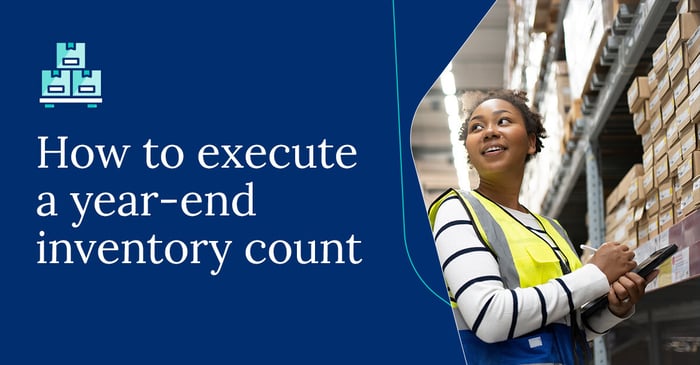
Year-end inventory plays a critical role for every type of business, from fashion to e-commerce to car manufacturing and everything in between. Not only does it provide insights about the previous year, but it also helps set the coming year up for success.
An annual inventory count is necessary for successful inventory management all year round. It allows you to clean up records and gives your business verified data to analyze.
Since retailers have a lot of inventory to manage, counting inventory correctly is crucial and allows you to make informed buying decisions later. Learn how to execute a year-end annual inventory count and how it can help forecast demand for the year ahead.
What is a year-end inventory count?
A year-end inventory count is a physical count of all the inventory on hand at the end of the year. You perform the count to verify that the physical inventory matches the numbers in your inventory management system.
An annual inventory count is different from an inventory cycle count, which audits a smaller portion of inventory. While a cycle count allows you to monitor your inventory by sampling your inventory throughout the year, a year-end inventory count is a physical count of everything you have on hand at one given point in time.
How do you conduct a year-end inventory count?
These are the steps you need to follow for inventory counting:
- Schedule your inventory count in advance. It’s crucial to pause your warehousing operations while counting to get an accurate snapshot of your inventory. You should plan a day that causes minimal impact on pausing the operations.
- Create a stock counting team. The team should be familiar with the inventory counting process and the areas they will be working in, such as a warehouse or storage room. Consider walking through the steps or even doing a dry run before the scheduled inventory day.
- Prepare your warehouse for the stock counting process. The warehouse layout should be clean and organized so counters don’t have to navigate around scattered inventory.
- Organize the warehouse by dividing it into count zones so each team has a clear area they are responsible for.
- Use the right counting tools. For manual counting, you can use counting tags, which are the physical labels used to count inventory. If you are using tags, then it’s best to let your team work in pairs so that one person can count the inventory while the other can note the values in the counting tag and stick it near the inventory. Get the counting tags signed by the respective team as it gives you clarity about the person associated with counting for a specific section.
- Cross-check count accuracy by personally examining the areas to cross-verify the values mentioned in the counting tags. Or, you can allocate members from other teams to cross-check the tag values. Cross-checking is crucial to get an accurate representation of your inventory. In case your inventory is also stored at other locations, you should coordinate to get the accurate values from those locations as well.
- Upgrade to an automated inventory management system. Performing inventory counts using manual sheets and counting tags can be time-consuming and prone to human errors. Using an inventory management software like Cin7 can be of great help. Instead of using tags and sheets, you can use barcode scanners to scan the inventories on the shelves. The software reconciles the inventory values with the ones already present in the system. This way, you can easily gauge the discrepancies in the inventory that’s physically present with you.
Why do a year-end inventory count?
The year-end annual inventory count is essential because it ensures the stock on your shelves matches your records. By getting an exact look at your inventory, you can comply with tax requirements, manage corporate audits, and offer accurate data to your accounting team.
Once you complete your inventory count, you’ll have the data you need to complete an annual financial analysis. The insights from the annual inventory count will not only help you make better business decisions for the coming year but will also show you if you’re dealing with inventory loss, such as shrinkage.
Knowing your year-end inventory allows you to:
- Get a clearer picture of what products you have.
- Hold accurate inventory records for accounting purposes.
- Learn from past sales data to avoid overstocking slow-moving products.
- Identify products that require a strategic shift to improve sales.
- Leverage data on demand and profitability to guide expansion plans.
- Consider adjusting periodic automatic replenishment (PAR) levels for top-selling products.
- Determine the cost of goods sold and total net income.
- Make business decisions based on data instead of intuition.
- Reconfigure pricing models to boost sales.
What is working inventory?
Working inventory, or work in process (WIP) inventory, is the inventory that is not yet completed. For calculating total inventory, WIP inventory is its own category, separate from other types of inventory, such as raw materials, finished goods, and maintenance, repair, and overhaul (MRO) inventory.
WIP inventory is calculated by subtracting the cost of the manufactured goods for the period from the manufacturing costs and beginning work in process amount from the same period. This requires gathering data from the previous period.
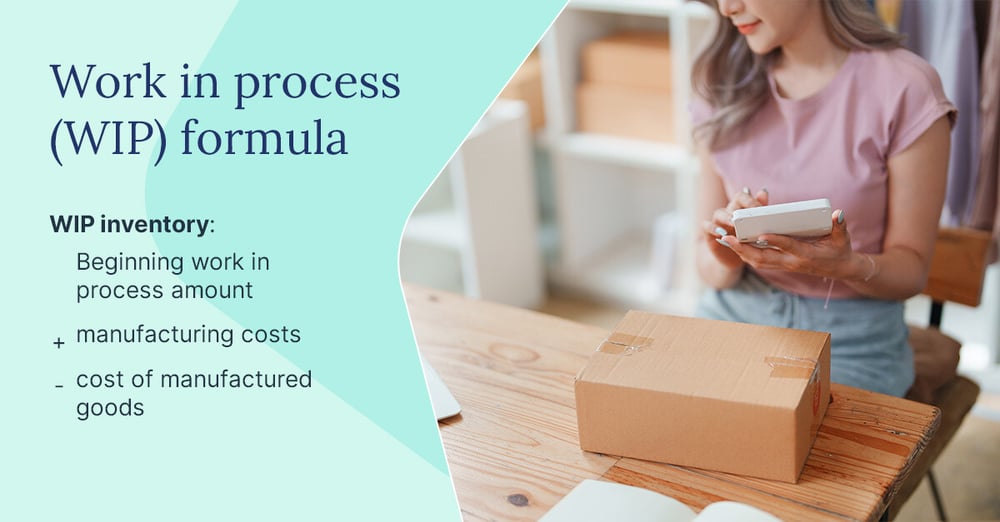
Does your business have inventory shrinkage?
Inventory shrinkage is essentially any inventory that’s missing, indicated by a discrepancy between inventory records and the physical inventory count. Shrinkage can be caused by any number of factors, such as:
- Human error
- Damaged stock
- Vendor shortages
- Lost inventory
- Theft
Shrinkage discovered in your year-end inventory count calls for investigation, as it can impact profits.
How to handle inventory shrinkage
Though many instances of shrinkage are unavoidable, such as damaged products, it’s still worth exploring potential causes. Inventory management software can provide you with insights into past records and trends so you can identify any ongoing patterns.
Small or one-time occurrences likely indicate a simple human error in recording inventory. Conversely, larger instances of shrinkage may indicate that your business is dealing with something more serious, such as widespread theft or even fraud.
After exploring potential causes, you’ll want to implement procedures to help prevent future shrinkage. This includes:
- Tightening security where inventory is stored
- Installing cameras or locking up high-value items
- Training employees about proper inventory counting
- Restricting access to new inventory to only trained employees
- Reviewing daily transactions on inventory apps
- Verifying the accuracy of purchase orders, invoices, and packing slips against received inventory
- Checking inventory shrinkage via cycle counts
What if you have too much inventory?
Having an excessive amount of inventory may require you to come up with strategies to deal with the surplus. If you’re still able to sell the excess inventory, you can then adjust plans, orders, and budgets accordingly.
How to reduce inventory
Here are some ways to reduce inventory:
- Determine your business needs for the year ahead.
- Decide on methods to get rid of the surplus, such as sales, discounts, repurposing, or donating. You may even be able to get a tax write-off for donated goods.
- A final option is selling excess inventory to a liquidator. This will come at a loss, but it will at least get rid of the surplus and free up space.
You should also consider inventory control methods to reduce the amount of inventory you have in stock. This includes:
- Using historical data to determine the minimum inventory needed to meet customer demand
- Calculating the reorder point, or the threshold for when goods need to be reordered. The reorder point formula is the average daily sold units multiplied by lead time.
- Utilize an inventory management strategy that helps keep track of inventory in every stage.
Using year-end inventory to predict next year’s demand
Conducting a year-end annual inventory count provides an overview of how your business utilized items throughout the year. This insight into usage can provide a basis for inventory forecasting for the coming year.
You can use inventory forecasts to help outline marketing campaigns, sales pushes, promotions, and more. Implementing forecasting will help move old inventory and enable you to focus on restocking only what your customers want.
Simplify inventory counts with Cin7’s inventory management software
Cin7’s inventory management software streamlines inventory tracking with cutting-edge technology and automation, giving you greater control and efficiency. Cin7 is the best choice for inventory management software because it helps save you time and money and reduces stress.
When you switch to Cin7, you’ll be able to:
- Access your data at any time and place.
- Set it up quickly, easily, and to your liking.
- Use ready-to-scan barcodes with your phone’s camera.
- Customize and allow access to teams, vendors, and suppliers.
- Generate custom barcodes for unlabeled stock.
- Understand your inventory with data-focused and shareable reports.
- Get alerts when you’re running low on a product, if it’s expiring, or approaching warranty.
- Create product histories to answer who, what, and when details.
Ready to see how our inventory software makes your year-end inventory count easier? Request a demo now.
FAQ
What is yearly inventory?
Your annual inventory count is the physical count of all inventory you have at the end of the fiscal year. In addition to keeping track of your stock with inventory management software, a physical count at least once a year ensures your inventory is accurate.
How do you do a year-end inventory count?
First, do a full count of all inventory. This includes all finished goods, raw materials, and WIP inventory. Next, note any potential discrepancies between your year-end count and other records. Then, cross-check all counts and verify the data. The final step is recording the inventory count.
How is inventory valued at the year-end?
Inventory is valued as ending inventory at year-end. Calculate it by subtracting the cost of goods sold (COGS) from the total cost of all goods that were available for sale.
Why is year-end inventory important?
Counting inventory at year-end ensures inventory records are accurate. Keeping accurate records is essential for ensuring you meet customer demand, record profits correctly, and have the data you need for financial analysis.
Is it good or bad to have inventory at the end of the year?
Unsold inventory impacts the amount of taxable income a business has and, therefore, the amount of money they are required to pay in taxes. It’s better to have less inventory left at the end of the year, as this reflects a higher COGS.