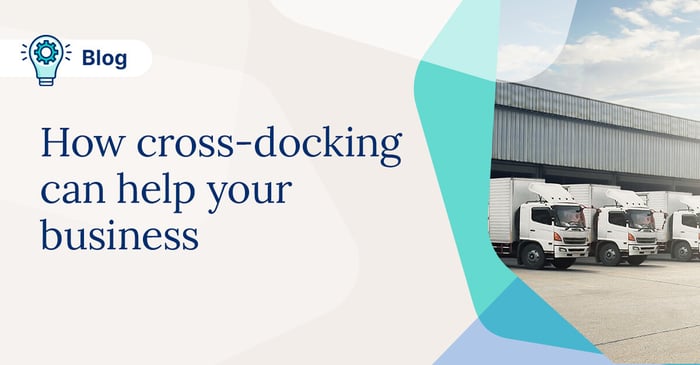
Supply chain efficiency is critical for success in today’s cutthroat business environment. As a result, companies are constantly seeking ways to optimize their supply chain operations, whether it’s by reducing inventory costs or speeding up delivery times.
One strategy that can help businesses accomplish some of these goals is cross-docking. Below, we’ll explain cross-docking, its main types and benefits, and some best practices to follow and keep in mind when integrating it into your supply chain.
Understanding cross docking
Cross docking is a business operational strategy that involves directly transferring incoming goods from inbound to outbound transportation with minimal to no storage in between.
This practice is aptly named “cross-docking” because goods literally “cross the docks”— from the receiving or inbound dock to the outbound or shipping dock in the shortest time possible.
Cross-docking occurs in several steps:
- Receiving: Inbound shipments arrive at a cross-docking facility or distribution center.
- Sorting: The goods are then sorted based on their final destination.
- Cross-docking: The sorted goods are then transferred from the receiving area to the outbound loading docks. This can be done using conveyor systems, forklifts, or even by hand.
- Outbound loading: The goods are then loaded directly onto outbound trucks, trailers, and other modes of transport for immediate delivery to their final destinations.
Conventional supply chains involve a warehousing step whereby the products are first stored — sometimes for days — before they are dispatched to their final destination. Cross-docking bypasses this step, significantly reducing the time products spend in the supply chain.
While a warehouse may still be present in a cross-docking operation, its function shifts from inventory storage to inventory coordination. Cross docking is particularly effective for high-demand, fast-moving products, ensuring they reach their destination quickly and efficiently.
Types of cross-docking
Cross-docking can be broadly categorized into two main types based on whether inbound goods are pre-tagged for specific destinations before they arrive at a cross-dock facility, or whether this is done at the facility.
Pre-distribution cross docking
In this approach, merchandise is dispatched from the manufacturing plant to the cross-docking facility with pre-determined instructions. This includes the final destinations of the products. So, the manufacturer is in charge of product distribution preparation, including attaching barcodes as well as labeling and pricing items.
Upon arrival at the cross-docking facility, the goods are simply unloaded, sorted according to the attached instructions, and then loaded onto outbound trucks for delivery.
The main benefit of this method is that it minimizes handling time at the cross-docking facility, ensuring quick delivery to stores. This might be crucial for seasonal items that need to be on shelves promptly.
However, pre-distribution cross-docking requires that the manufacturer knows the demand quantity for each store and labels products accordingly.
Post-distribution cross docking
This method differs by postponing the sorting of goods until the final destination is chosen, based on factors such as demand. This approach means that goods tend to spend a slightly longer time at the distribution center.
However, post-distribution cross-docking offers one key advantage — flexibility. The business can adapt to changing market conditions and optimize stock levels at each store based on real-time demand, forecasts, or sales trends.
Cross-docking benefits
Cross-docking offers a multitude of advantages that can significantly enhance your supply chain’s efficiency and profitability. Let’s explore these benefits:
Reduced inventory costs
The most obvious benefit is the reduction in inventory costs. Cross-docking minimizes the need for storage, as products are quickly transferred from inbound to outbound transportation without lingering for extended periods in a warehouse. The savings on warehousing space alone can be substantial, especially for businesses that handle large volumes of goods. Reduced storage needs also mean lower utility costs and less need for security measures to protect stored goods.
Cross docking also saves labor-related costs, as inbound materials don’t need to be unloaded, stored, and then retrieved later and loaded onto outbound vehicles.
These cost savings from cross-docking can be used to fund other important business areas, such as research and development or customer service.
Reduced inventory holding risks
Another significant benefit of cross-docking is the reduced risk associated with holding inventory. Products move quickly through the supply chain, reducing the time they are exposed to potential damage, deterioration, or even obsolescence. In a nutshell, cross-docking helps maintain product quality and lowers the risk of losses due to spoilage or degradation.
Faster delivery times
Since products bypass storage and are shipped out quickly, cross-docking leads to faster delivery times. This can give businesses a competitive advantage by meeting customer expectations for rapid product delivery.
Improved accuracy
Traditional supply chains involve multiple product handling steps (receiving, storing, picking, packing, shipping). Each step introduces a potential point of error, such as mislabeling, misplacement, or incorrect picking. Cross-docking minimizes these touchpoints, significantly reducing the likelihood of such errors.
Enhanced responsiveness
The ability to adapt swiftly to customer needs and market fluctuations is a critical competitive advantage in today’s business landscape. Cross-docking facilitates this responsiveness in two key ways:
- Reduced lead times: Since products don’t go into storage in a cross-docking operation, lead times are significantly reduced. This allows businesses to react more quickly to changes in demand.
- Inventory flexibility: As discussed earlier, post-distribution cross-docking allows for delaying sorting until final destinations are identified. This flexibility empowers businesses to adjust product allocation based on real-time demand fluctuations. By fine-tuning the flow of goods to stores in real-time, businesses can maintain optimal inventory levels, avoiding the costs of excess stock or missed sales opportunities.
Increased sustainability
Cross docking contributes to a more sustainable supply chain in the following ways:
Reduced energy consumption
Larger storage facilities usually require substantial energy for lighting, heating, and cooling. By minimizing the need for long-term storage, cross docking significantly cuts down on these energy requirements. This lowers the carbon footprint of a business’s supply chain operations, which translates to a more sustainable business model.
Minimized packaging waste
In a conventional warehousing system, products may be repackaged multiple times as they move through different stages of storage and handling. This repeated packaging not only generates waste but also increases the consumption of materials such as cardboard, plastic, and other packing supplies.
Cross docking streamlines the movement of goods with fewer storage and handling points, reducing the need for excessive packaging and, by extension, minimizing waste generation.
Best practices for implementing cross docking
Having seen the benefits of cross-docking, you might be considering integrating it into your supply chain.
Here are some key best practices to keep in mind for a successful implementation:
Suitable products for cross-docking
Some products are more suitable for cross docking than others. Here are some products that might be ideal candidates for this approach.
- High demand/fast moving: These are products that sell quickly and constantly need to be restocked. Cross-docking minimizes storage time and expedites their delivery to stores.
- Perishable goods: Due to their short shelf life, products such as fresh produce, dairy, meat, and other perishables are also ideal candidates for cross-docking. Minimized storage and faster movement through the supply chain ensure these goods reach customers while still fresh.
- Seasonal or promotional goods: These are items that have peak demand for a limited window and thus require rapid delivery to stores. Cross docking can facilitate that.
- Standardized products: Products with consistent packaging, labeling, and weight are easier to handle and sort within a cross-docking facility, making them ideal for this process.
- High-cost or high-value items: High-value or expensive products can also benefit from cross docking due to reduced risk of theft, spoilage, and obsolescence associated with long-term storage. Faster movement through the supply chain safeguards their quality and value and ensures timely delivery.
Working with a third-party logistics (3PL) partner
You can set up your own cross-docking operation if you have the resources, including space, staff, and technology. However, many businesses, especially small businesses, choose to work with a third-party logistics (3PL) partner. Not all 3PLs are created equal, so it’s important to conduct due diligence to ensure you select the right partner for your needs. Here are some factors to consider.
- Expertise and experience: The 3PL partner you select should have extensive experience and expertise in cross docking operations. This includes a deep understanding of logistics management, inventory control, and efficient handling of diverse product types. An experienced partner will have established processes and systems in place to ensure smooth cross docking, minimizing delays and errors.
- Technological capabilities: Effective cross-docking relies heavily on advanced technology. Look for 3PL partners that use state-of-the-art warehouse management systems (WMS), transportation management systems (TMS), and real-time tracking and monitoring tools. These technologies enhance supply chain visibility, enabling better coordination of inbound and outbound shipments, and guaranteeing accurate and timely product delivery.
- Strategic location: The location of the 3PL’s facilities is another important factor to consider. A strategically located cross-docking facility can significantly reduce transportation costs and delivery times. Ideally, the facility should be close to major transportation hubs, such as railways, ports, or highways, ensuring easy access for both inbound and outbound shipments.
- Scalability and flexibility: A good 3PL partner should offer flexible and scalable solutions that can accommodate evolving business needs. As your business grows or experiences seasonal fluctuations, the partner should be able to adjust operations accordingly, including handling increased volumes or different types of products without sacrificing efficiency.
- Great track record: Evaluate the track record of potential 3PL partners. Prioritize partners with proven success in managing cross-docking operations for businesses similar to yours. References, case studies, and client testimonials can provide valuable insights into their performance and reliability.
- Diverse service offerings: A well-rounded 3PL partner should offer a range of logistics services that complement cross docking. This might include transportation, order fulfillment, and value-added services like kitting, packaging, and labeling. A comprehensive service portfolio ensures that all your logistics needs are met through a single provider, simplifying management and coordination.
- Strong communication and collaboration: Effective communication and collaboration between your business and the 3PL partner are crucial for successful cross docking. The partner should have robust communication channels and a collaborative approach. This ensures both parties are aligned on objectives, expectations, and any issues that may arise.
Additional considerations for a successful cross docking implementation
Beyond selecting the right products and partnering with a qualified 3PL provider, a successful cross-docking implementation also hinges on several key elements:
- Precise coordination: Precise coordination across the entire supply chain is paramount. This includes seamless integration between your operations and the 3PL partner’s systems, ensuring smooth information flow and efficient execution.
- Real-time data sharing: Real-time data sharing is crucial for informed decision-making. The ability to access real-time inventory levels, shipment tracking data, and other critical information empowers you and your partner to optimize operations and proactively address potential issues.
- Timely transportation: Reliable and timely transportation is an essential link in the cross-docking process. Consistent on-time pick-ups and deliveries are vital for maintaining efficient product flow and minimizing delays throughout the supply chain.
Wrapping up
Cross-docking offers a compelling strategy for businesses seeking to streamline their supply chains and potentially improve efficiency. This approach can yield several advantages, including reduced inventory costs, faster delivery times, enhanced accuracy, improved responsiveness to customer needs, and increased sustainability in the supply chain.
However, successful cross-docking implementation requires careful planning and execution. Part of this is confirming your products are a good fit for the strategy. The other one is partnering with a qualified 3PL provider.
Cin7 can be a valuable partner in this process. Our in-house team of 3PL experts can offer valuable guidance and help you choose a partner that perfectly aligns with your business needs. Cin7 Omni provides native integrations to popular 3PL companies, freeing up your team and ensuring real-time communication between your inventory system and your 3PL. But that’s not all! With solutions like automated order rerouting, real-time inventory visibility, and enhanced communication tools, Cin7 inventory management software can help you unlock the full potential of your partnership with a 3PL partner.
Start your free trial today.
More from the blog
View All Posts
Top E-Commerce Inventory Management Techniques and Optimizing Inventory Control With Cin7
Read More
Complete Guide to Inventory Management: Types, Efficiency and More
Read More