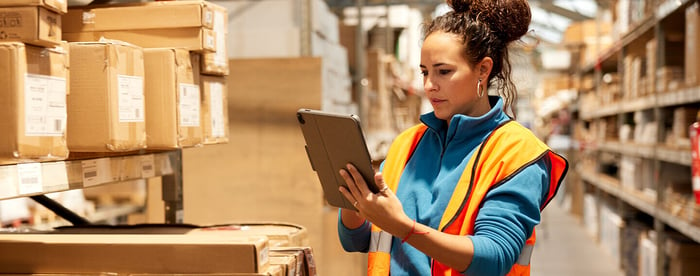
We all know the excitement of waiting for a package to arrive — and the confusion and disappointment when a delivery gets delayed.
Customers remember brands that deliver their products quickly. If an order takes weeks to arrive, customers will likely think twice before ordering from that company again. Brands that prioritize quick order fulfillment build trust and reliability with their customers.
Manufacturing lead time refers to the time between when the production of a product is scheduled and when it’s completed — it’s a major factor in driving consumer trust and happiness.
If you’re outsourcing products, much of the lead time is out of your control since you’re relying on the supply chain. However, as a business owner, there are actions you can take to mitigate supply chain issues and reduce manufacturing lead time.
In this post, we’ll explore the different factors that impact manufacturing lead time and provide tips on how to reduce it.
Key Takeaways:
- Lead time begins when a customer places an order, whereas cycle time starts once work begins on a product.
- Calculate manufacturing lead time by adding preprocessing time + processing time + post-processing time.
- Numerous factors impact manufacturing lead time, such as stockouts, lead time variability, delays in shipping, and more.
- Automating your inventory management process is a great way to reduce lead times and get products delivered quicker.
Types of lead time
In the manufacturing process, there are four primary types of lead time that relate to the process as a whole. These include:
- Customer lead time: The time it takes for a customer to receive an order after they place it.
- Material lead time: The time it takes for a company to receive raw materials after becoming aware that they need them.
- Production lead time: The time it takes for a company to manufacture a product after receiving its materials.
- Cumulative lead time: The sum of the three lead times listed above.
All of these lead times work in tandem to determine the total lead time required to manufacture and deliver the product.
Lead time vs. cycle time
Lead time and cycle time are commonly confused, but you can distinguish them by looking at the timeline for an order.
While lead time begins when a customer places an order, cycle time doesn’t begin until work actually begins on the product. So while lead time includes both purchase processing and the actual manufacturing, cycle time only refers to the process once manufacturing begins.
How to calculate manufacturing lead time
To reduce manufacturing lead time, you have to know what your baseline is. Luckily, you can easily calculate manufacturing lead time so you can make a plan to reduce it.
The formula for calculating manufacturing lead time is:
While this calculation may appear simple, it’s important to know exactly what each term refers to before crunching the numbers. Here’s what each element means:
- Pre-processing: The time it takes for a company to process a customer order, obtain supplies, and prepare the supplies for production.
- Processing: The time it takes to produce the order (this is the same as cycle time).
- Post-processing: The time it takes to deliver the product to the consumer.
Adding these elements together paints a full picture of the manufacturing process — and the timelines for each step. It’s important to break the equation down into these three timelines so you know which step to prioritize first when optimizing your lead time.
What impacts manufacturing lead time?
Knowing how to calculate and reduce manufacturing lead time is significant because of the sheer amount of factors that can add to or increase lead time. The factors that impact manufacturing lead time include but are not limited to:
1. Stockouts
Just as a vehicle cannot run without fuel, a manufacturer cannot fulfill orders without raw materials. Stockouts can be catastrophic for manufacturers as they bring production to a halt. This delay in production can:
- Increase lead time.
- Add to customer dissatisfaction.
- Reduce sales.
- Incentivize customers to buy from competitors.
With the right inventory management software, you can set reorder points so the system will automatically place orders with suppliers when raw materials fall below a certain preset level, ensuring that you do not face stockouts.
Learn how Cin7 inventory management solutions solves this problem and more with a live demo.
2. Lead time variability
Just as stockouts can lead to an increase in manufacturing lead time, the same can happen with suppliers. Stockouts and supply chain issues with suppliers can increase their lead time, leading to an increase in yours.
Dealing with multiple suppliers can make predicting when all required items will be delivered difficult, resulting in overstocking or understocking. Ordering excess inventory can strain your budget while understocking can lead to a loss in potential sales. All of this makes it challenging to execute production smoothly.
You can address this issue by consolidating suppliers to ensure that everything you need arrives simultaneously, allowing for smooth production runs and lower shipping costs.
3. Amount of testing required
If you plan to go skydiving, you expect the parachute to be well-tested and of supreme quality, right? After all, your life depends upon it.
For items like parachutes, extensive testing is essential, and more testing requires more time. The production part approval process (PPAP) determines the time to complete processing. In manufacturing, you need to check the individual quality of the products and ensure the parts work as desired once combined.
The number of tests — and the number of parts you must test — all affect lead time.
4. Delays in shipping
Shipping is the act of carrying items from one place to another. A number of factors can affect shipping time, including natural disasters, human error, and component shortages. Out of all the issues discussed so far, this one is the most unpredictable and challenging to control.
Businesses can mitigate the risk of shipping delays by sourcing suppliers located nearby. Otherwise, you can choose a supplier who constantly keeps inventory stocked by monitoring their levels. There’s a general rule of thumb: Fewer incoming shipments lead to a lower risk of order fulfillment delays.
5. Inefficient inventory control
Inefficient inventory control can adversely affect the lead time of your manufacturing unit. Inefficiencies increase inventory management costs, raise stock handling charges, and generally slow the production process. Unlike delays in shipping and lead time variability of suppliers, inventory control is entirely in your control.
Implementing proper inventory control can help you determine how much inventory you currently hold, ensuring that you have all the necessary components to run manufacturing smoothly.
6. Market demand
In 2017, the demand for fidget spinners was soaring high. It is estimated that 50 million fidget spinners were sold in the first half of 2017 alone. But today, hardly anyone talks about them.
This case proves that you cannot perfectly predict customer demand. If something is highly sought after today, it does not necessarily mean that it would be relevant tomorrow. Improper demand planning in such scenarios can lead to losses.
Market demand can also affect the lead time. If there is a spike in demand for your product, your suppliers could likely face high demand as well. A delay from suppliers can increase order fulfillment time and increase your lead time.
How to reduce manufacturing lead time
Reducing lead time can make for happier customers and build compounding trust. As a result, it’s paramount to know how to combat supply chain disruptions and ensure you’re optimizing manufacturing lead time. Some methods include:
1. Keep safety stock
If you don’t use just-in-time inventory, then keeping safety stock is a great buffer in case supply chain disruptions arise. Safety stock is inventory that a company sets aside to avoid a stockout.
In industries where it’s impractical to keep excess stock on hand, consider setting reorder points, which is the level at which stock needs to be replenished. If you use inventory management software, you can set custom reorder points so stock will automatically reorder when it reaches a specific level.
2. Order in smaller quantities
Ordering smaller amounts more frequently allows you to fulfill orders quicker than if you placed larger bulk orders.
By breaking up invoices into smaller quantities, you can quickly dispatch orders and reduce your manufacturing lead time. Although you may receive supplier discounts by ordering in bulk, it is often more efficient to order smaller quantities.
3. Put lead time in your contract
If you’re expecting your supplier to send your products within a certain time, put it in writing. When delays happen and you’re unable to fulfill orders on time, it can be a major detriment to your business.
Your contract with your supplier should clearly state the expectations for timing and the penalties for late shipments. Without a clear line of communication or set expectations, delays can easily occur.
4. Streamline your process
If you’re looking for ways to reduce manufacturing lead time, it may be helpful to first examine your own processes and the steps you can condense or eliminate.
Some ways you can streamline your processes may include:
- Completing tasks in parallel
- Eliminating repetitive QA processes
- Automating your sales orders
5. Automate your inventory management system
Automating your inventory management eliminates the chance of manual error in your process and, in turn, reduces the chances of delays and setbacks in your manufacturing process.
While spreadsheets can accomplish a lot, automated inventory management can alert you when inventory is low, automate vendor management processes, create purchase orders and shipping labels, and more. Automating all these elements of the production process can help your business run as smoothly as possible.
Request a demo of Cin7 Core to see automated inventory management in action.
What are the benefits of reducing manufacturing lead time?
Getting products to consumers on time leads to happier customers, but businesses have more on the line than just retaining customers when it comes to lead time. Here are a few other benefits that come when you reduce manufacturing lead time:
1. Prevents against dead stock
Dead stock, or inventory that gets manufactured but goes unsold, can occur if businesses can’t sell their products to customers in a timely manner. Reducing manufacturing lead time fights against excess inventory that can often be very costly to a business.
2. Makes for greater output
If you can get orders to customers quicker, you’ll be able to field more orders and generate more sales. Reducing manufacturing lead time can increase profits as it enhances the number of orders a company can handle.
3. Creates a more efficient use of capital
The longer capital is tied up in raw materials and production, the longer a business has to wait to generate a profit from its sale. By reducing manufacturing lead time and enhancing orders and sales numbers, companies can gain profits faster — thus allowing them quicker growth.
4. Builds trust and satisfaction
Customers are more likely to trust and return to a business that will always have products in stock and will deliver quickly. Companies that shorten manufacturing lead times reap the benefits of happy customers and have an easier time gaining new business.
Why are manufacturing lead times so long?
Factors inside and outside of your control can prolong manufacturing lead times. Consider the last three years for instance, when lead times extended due to external factors — like COVID-19, global conflict, and inflation.
However, internal errors can prolong manufacturing lead times as a result of errors by companies, from misuse of material to insufficient labor or an inability to transfer finished goods to warehouses for distribution.
Getting products out on time requires many different departments to move in sync, and it can be difficult to keep track of. Inventory management software simplifies this by keeping processes in a centralized space, and automating most of them, so you can always keep a pulse of the manufacturing process.
Looking to reduce lead times and gain customers? An inventory management software solution can help. Start a free trial of Cin7 Core to see how we can help.
More from the blog
View All Posts
Best Practices for Inventory Organization
Read More
Proactive Strategies to Mitigate Supplier Risks and Disruptions
Read More