Mastering Lean and Agile Supply Chains: Balancing Efficiency and Flexibility
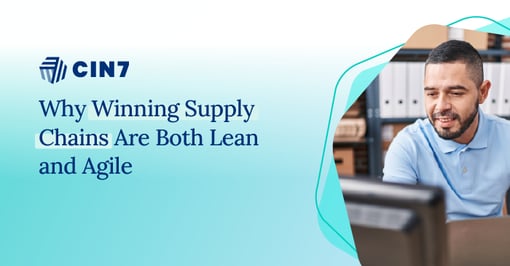
When businesses are building their supply chain strategy, they most often have to choose between two primary approaches. These are a lean supply chain, which emphasizes efficiency and cost control, and an agile supply chain, which focuses on flexibility, responsiveness and adaptability.
The choice isn’t always black and white. On one hand, efficiency, which includes cutting waste and optimizing workflows can unlock significant savings, which could be critical in industries where margins are razor-thin. On the other, volatile markets and unpredictable consumer behavior demand agile systems that can pivot quickly, even if it means higher operational costs.
Some businesses may find success by committing fully to one model, while others may need a hybrid strategy that balances both efficiency and adaptability.
Ultimately, understanding the differences between these two approaches is essential for businesses aiming to align their supply chain strategy with their unique industry dynamics, as well as their internal goals, needs, and preferences.
In the following sections of this guide, we’ll break down the core principles behind each approach, compare advantages and challenges, and outline unique scenarios where one model may be better than the other.
What is a Lean Supply Chain?
The lean supply chain model prioritizes efficiency by minimizing all forms of waste or inefficiencies in the supply chain. This includes excess inventory, overproduction, waiting times, unnecessary transportation, overprocessing, unused talent, and defects.
Lean principles are rooted in the Toyota Production System (TPS). Developed by the Japanese automaker after World War II, the TPS aimed to optimize production processes by systematically identifying and eliminating waste. This philosophy has since been adapted and applied to supply chain management.
The primary goal of lean is to maximize customer value (i.e., good quality products) with minimal resource expenditure. This is achieved through principles like Just-in-Time (JIT) production, which aims to deliver materials and products exactly when needed, reducing storage costs and waste.
Besides waste elimination, another fundamental component of the lean model is continuous improvement (kaizen in Japanese), which involves regularly evaluating processes and making incremental improvements to achieve even more efficiency and cost effectiveness.
Lean principles also include establishing standardized processes to minimize variations and improve consistency.
Advantages of the Lean Model
- Cost efficiency: Lean minimizes operational expenses by eliminating waste (such as excess inventory and overproduction) and optimizing resource usage.
- Continuous improvement: Lean encourages a culture of kaizen, which are incremental process improvements that lead to overall operational excellence.
- Streamlined operations: By eliminating non-value-adding activities and focusing on process optimization, lean supply chains ensure smoother and more efficient workflows.
- Predictability & stability: Lean systems allow for consistent production and predictable lead times.
- Quality control: Standardized processes contribute to consistent product quality and can lead to a reduced number of defects.
Disadvantages of Lean Models
- Limited flexibility: Lean supply chains are less adaptable to sudden market fluctuations or unpredictable consumer demand.
- Vulnerability to supply chain disruptions: Since one of the core principles of lean systems is minimizing or even completely avoiding excess inventory, any supply chain interruptions (such as delays from suppliers) can halt production, leading to stockouts.
- Not ideal for high-variation demand: Industries with high variability in demand or product cycles may find lean strategies difficult to effectively implement.
What is an Agile Supply Chain?
While lean supply chains focus on efficiency, agile supply chains prioritize speed, flexibility, and real-time responsiveness. The latter are designed to be highly-responsive and adaptable to unpredicted changes in the supply chain and market environments. This involves having systems or processes in place that allow a company or business to pivot quickly—whether to capitalize on a viral trend, navigate a raw material shortage, or meet a sudden surge in orders.
Common agile practices include maintaining strategic inventory buffers, diversifying supplier networks, and investing in technologies like AI-driven demand forecasting.
Although agile models might incur higher operational costs due to flexible logistics and stockpiling, they’re indispensable in industries where customer expectations can shift overnight, like tech or e-commerce, and other sectors where supplier disruptions are common.
Take Zara, for instance. The fashion giant designs, produces, and delivers new collections in just 2–3 weeks— a significantly faster turnaround than traditional retailers who can take months. This agility lets Zara capitalize on trends before competitors.
Advantages of Agile Models
- High responsiveness: Agile supply chains can adjust quickly to fluctuating market demands and customer preferences.
- Resilience: Through strategies like maintaining strategic inventory buffers and diversifying suppliers, agile supply chains are more able to absorb shocks and disruptions like natural disasters or geopolitical crises.
- Better customer satisfaction: The ability to meet changing demand or consumer preferences quickly improves service levels, which can lead to higher customer satisfaction and loyalty.
Disadvantages of Agile Models
- Greater costs: Maintaining flexibility comes at a cost, including higher inventory, expedited shipping, and multiple supplier arrangements, all of which can drive up operational costs.
- Risk of inventory obsolescence: Maintaining higher levels of inventory to meet fluctuating demand can lead to excess stock or unsold products, particularly in industries with short product life cycles.
- Complexity in management: Maintaining an agile system requires sophisticated monitoring, real-time data analytics, advanced forecasting and flexible supply chain management processes, all of which increase operational complexity.
Lean vs Agile Supply Chains: Key Differences
Let’s look at the main differences between lean and agile systems
Element |
Lean Supply Chain |
Agile Supply Chain |
Philosophy and Focus |
Focuses on eliminating waste and maximizing efficiency by streamlining processes and minimizing non-value-added activities. |
Prioritizes flexibility and responsiveness, aiming to quickly adapt to changes in customer demand, market conditions, and disruptions. |
Inventory Management |
Minimizes inventory levels by using strategies like Just-In-Time (JIT) to reduce holding costs and avoid overstocking. |
Maintains higher levels of inventory or uses flexible sourcing strategies to ensure that the supply chain can quickly meet sudden changes in demand. |
Customer Demand |
Best for environments where customer demand is stable, predictable, and consistent. |
Ideal for environments with unpredictable, fluctuating, or seasonal demand. |
Lead Times |
Reduces lead times through efficiency, but may be slower to adapt to changes. |
Focuses on minimizing lead times by keeping the supply chain flexible and responsive. |
Supply Chain Relationships |
Prioritize long-term, stable relationships for efficiency. |
Flexible, transactional, and more dynamic relationships with suppliers for adaptability. |
Risk Management |
Reduces risks through efficiency, but can be vulnerable to disruptions like supply shortages. |
Emphasizes the ability to quickly adapt to risks such as supply disruptions, market shifts, or sudden demand spikes. |
Cost Structure |
Aims to lower operational and inventory holding costs through streamlined processes. |
May incur higher costs for flexibility and quick adaptation to changes. |
Implementation |
Lean supply chains require careful planning, process standardization, and continuous improvement. They work best in stable environments where predictable demand allows for streamlined operations and efficiency improvements. |
Agile supply chains require robust communication, technology, and fast decision-making. They thrive in dynamic environments where the ability to quickly change processes or reconfigure strategies is necessary to meet fluctuating demands. |
Choosing the Right Supply Chain Model for Your Business
Selecting the right supply chain model between lean and agile depends on a variety of factors specific to your business. By analyzing these factors, you can determine which supply chain approach will best align with your goals for efficiency, flexibility, and customer satisfaction.
Here are the factors to consider when making your decision.
Product Type
Lean systems are ideal for standardized, high-volume products with long life cycles (e.g., household appliances, automotive parts). These items come with predictable demand and have minimal customization requirements.
Agile systems are better suited for customized, niche, or trend-driven products (e.g., fast fashion, limited-edition electronics). Agile accommodates rapid design changes and short life cycles.
Demand
If demand for your products is stable and predictable, a lean supply chain can help maintain efficiency and reduce costs through precise production planning and inventory control.
If demand is volatile and unpredictable, an agile supply chain is necessary to enable rapid response to market changes.
Market Volatility
Lean principles fit industries with steady competition and slow-changing trends such as automotive and utilities. Conversely, agile principles are necessary in fast-moving sectors (e.g., electronics, fast fashion) where competitors can disrupt the market overnight.
Cost Sensitivity
Lean principles are ideal for businesses where low prices are a key selling point, such as discount retailers or bulk goods. Lean’s waste reduction keeps costs—and prices—competitive. Agile principles are best for brands where customers accept premium pricing for speed or exclusivity — for example luxury goods and custom furniture.
Lead Time Requirements
Lean principles work best when lead times are predictable and long, such as heavy machinery, construction materials. On the other hand, agile principles are better for industries requiring rapid turnaround, e.g., e-commerce and emergency medical supplies.
Production Flexibility
If your products have fixed designs and require long-term production planning, a lean supply chain ensures maximum efficiency through standardized manufacturing processes.
If you need to frequently adjust production processes to accommodate new models or limited-edition products, an agile supply chain will provide the necessary flexibility for rapid changes.
Company Culture
Lean supply chains are best for companies with a culture focused on efficiency, cost reduction, and continuous improvement. Agile supply chains work well in organizations that value innovation, adaptability, and rapid decision-making. Agile cultures encourage experimentation and the ability to change strategies quickly and as needed.
Supply Chain Complexity
Lean principles are ideal for simple, localized supply chains with fewer variables. The model’s focus on minimizing waste works when suppliers, production, and distribution are tightly controlled.
Agile principles, on the other hand, are necessary for complex, multi-tier supply chains that include multiple suppliers, cross-border logistics, and diverse product lines, for example. Agile’s flexibility helps manage unpredictability in all these variables.
Using Hybrid Models
Both lean and agile principles have their strengths and best use cases as we’ve seen. However, many businesses find success with a hybrid approach that combines the strengths of both systems.
The hybrid approach allows companies to balance efficiency and flexibility. It can be particularly valuable for businesses that face both stable and fluctuating demand, or those operating in industries with varying levels of product lifecycle or demand predictability.
Companies like Zara and Nike have successfully implemented hybrid supply chains. They apply lean principles in areas with predictable demand, such as core fashion and footwear styles that see consistent sales, while maintaining agility in response to fashion trends or sudden shifts in consumer preferences. This dual approach allows them to keep costs low in stable product lines, while staying responsive and flexible in more volatile segments.
How Businesses Can Integrate Both Models
- Technology: Leveraging advanced technology, such as AI-driven demand forecasting, plays an important role in merging lean and agile strategies. AI can predict shifts in customer demand with high accuracy, allowing businesses to make real-time adjustments to inventory levels, production schedules, and distribution channels. This ensures the supply chain remains efficient while staying responsive to market changes.
- Flexible supplier relationships: Companies might keep long-term relationships with core suppliers for stable, lean operations, while also maintaining a network of backup suppliers for more agile responses to changes in demand.
Key Benefits of a Hybrid Approach:
- Achieves a balance between cost-efficiency and flexibility
- Enhances the ability to respond quickly to market changes without sacrificing operational cost savings
- Provides a versatile supply chain that can adapt to different types of demand.
Best Practices for Implementing Lean and Agile Supply Chains
Regardless of which supply chain model you opt for, the following best practices will help you achieve the best possible outcomes.
Leverage Technology
Implementing AI and machine learning algorithms can provide accurate demand predictions, allowing for optimized inventory levels and production schedules. This helps in minimizing waste, which is a key lean principle, while also allowing for quick adjustments to unexpected demand changes, which is a key agile principle.
In addition, technologies like IoT sensors, blockchain, and cloud-based inventory management platforms like Cin7 provide real-time visibility into the entire supply chain. This allows businesses to minimize waste, identify potential disruptions early, and quickly pivot operations.
Meanwhile, automating processes in fulfillment centers, such as robotic picking, packing, and sorting, significantly speeds up order processing and reduces errors in lean environments while freeing up resources for agile teams to focus on innovation.
Train Your Teams
Equip your team with the knowledge and skills to understand and apply lean and agile principles. Focus on data analysis, problem-solving, and the use of relevant technologies. Empower them to make informed decisions and contribute to continuous improvement initiatives.
Continuously Learn and Improve
Regularly assess your processes, gather feedback from teams, and implement changes that enhance productivity and reduce bottlenecks. Embrace a mindset of constant iteration, which helps you adapt to challenges while consistently improving performance.
How Cin7 Helps Businesses Optimize Their Supply Chain Strategy
Cin7 is a powerful platform designed to help businesses optimize their supply chain operations. Here’s how Cin7 can support both lean and agile supply chain models.
Real-Time Inventory Visibility for Lean & Agile Models
Cin7 provides businesses with real-time inventory tracking and visibility across multiple warehouses and fulfillment centers. This feature is crucial for businesses implementing either lean or agile supply chains. For lean supply chains, Cin7 helps optimize inventory levels and minimize holding costs by providing clear visibility into stock availability, order status, and warehouse performance. For agile supply chains, Cin7’s real-time updates allow businesses in volatile markets to stay responsive to demand shifts and adjust stock levels accordingly, ensuring they meet consumer needs promptly without overstocking.
AI-Powered Demand Forecasting
Cin7’s AI-driven demand forecasting tool enables businesses to predict customer behavior and anticipate demand fluctuations, which again is a critical element in both lean and agile supply chains.
For lean supply chains, accurate forecasts help streamline production planning, reducing waste and ensuring inventory levels align with expected demand. For agile supply chains, Cin7’s real-time demand forecasting provides the flexibility to quickly adjust to changes in demand, allowing businesses to stay ahead of market trends and avoid stockouts.
Seamless Integration Across Sales Channels
Cin7 enables seamless integration across all sales channels, from e-commerce platforms to physical stores, creating a unified approach to managing inventory, sales, and fulfillment.
For lean supply chains, this integration ensures that businesses can manage their stock levels efficiently, ensuring that resources are directed where they’re needed most. For agile supply chains, real-time synchronization between sales channels enables businesses to react faster to changes in customer demand, whether through online or in-store orders. This flexibility enhances responsiveness while maintaining operational efficiency.
Schedule a demo to see how Cin7 empowers your business to master lean, agile, and everything in between.
More from the blog
View All Posts
Just in time inventory (JIT): Definition + benefits in 2024
Read More
Wholesale Distribution Challenges
Read More